文/黃靖萱/商業周刊
在被養殖魚場、眾多小型鐵皮鐵工廠包圍的鄉間,我們看見台灣螺絲界智慧工廠跑最快的廠商:世豐。
6年多前,陳駿彥接下父親的棒子升任總經理,但就在當年,因美國貿易商和全球最大家具建材零售商家得寶在物流的配合不順,原本高峰時可占世豐6成營收的家得寶,預告世豐2013年訂單到期後,將不再續約。
為了彌補營收大洞,新手總經理陳駿彥立刻開始全球跑透透找客戶,嚴峻的管理挑戰也伴隨而來。
原來,世豐供應家得寶只有24種品項,工廠只要大批量的生產就過關,但一下湧進120個客戶的上萬種品項,所有流程,只能用混亂兩字來形容。
「我發現,我們員工不太能Handle這麼複雜的狀況,」陳駿彥很無奈,那段時間,世豐的工廠常做不出客戶要的產品,反而不斷去鞠躬道歉。「再這樣下去,我跑更多客戶回來也沒用。」
痛定思痛後,「唯一能改的就是用系統,把他們框住,」陳駿彥說。
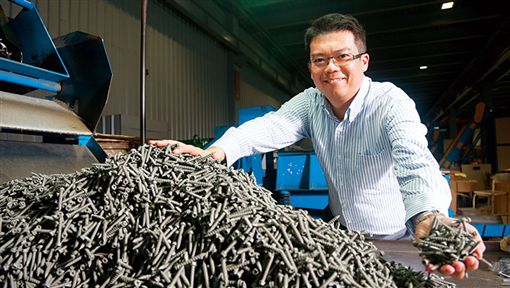
▲世豐螺絲總經理陳駿彥。(圖/駱裕隆攝影/商業周刊)
若不計世豐在2011年就導入只有台積電、鴻海等大廠才捨得花錢的企業資源規畫(ERP)系統。去年世豐甫投入自動排程系統及初期的製造執行系統(MES)金額,就相當前一年淨利的1/5。
但陳駿彥遭遇的阻力不在於金錢,而是來自現場的黑手師傅。
因為買來的系統是空的,必須要鍵入各種參數,才能讓系統知道世豐在排程上的需求及邏輯,這,必須要靠師傅們將經驗傳授給電腦。
但,一開始師傅們非常抗拒,覺得電腦要搶走他們的工作,陳駿彥只能不斷跟師傅保證,電腦是在減輕他們的工作負擔。師傅反而可升級專心做品質檢測,並成為這群機台的「管理者」。
一來一往,他要說服師傅們,他們並不是被電腦制約,而是電腦聽命於他們。
這場革命後,讓世豐可以有條不紊的管理上萬種品項的生產,還有效降低浪費。
為了串聯生產,世豐在150部機台裡都加裝感測器及電腦。過去,當客戶下單後,因為動輒百萬支的量難以計算,世豐都為預防耗損,會再多加5%的重量去生產。每一次,都得等到包裝完,才發現多生產了上萬支螺絲。
光是2015年,就有高達1,200萬支螺絲,被當成廢料銷毀。
而且,以前都是每做完一批,就由師傅手寫,交給助理輸入到電腦裡,但是因為客製化造成訂單量大,且越來越複雜,「一下是重量輸入錯,一下是訂單號碼輸入錯,出錯的機率超高,」世豐螺絲發言人王新元說。
現在,機台裡的感測器精準計算生產的螺絲數量,才導入半年,去年世豐銷毀的螺絲數量已減少了1/3。
去年,有初步成效的世豐,獲利創近5年新高,淨利率是螺絲大廠春雨的2倍。
現在,世豐還進一步將上萬個生產模具的資料建檔,以預測模具什麼時候會壞。
跟多數製造商相同,過去,世豐無法知道每個模具的壽命還剩多少,常是師傅看到生產出來的螺絲品質不對了,才停機換模。
現在,世豐把每個模具的壽命值蒐集後。未來,系統就能聰明做到模具和訂單的匹配,如某筆訂單只要20萬支,就指定某個模具剛好剩20萬支壽命的模具來生產,更進一步精準管理。
【更多報導】
香蕉給得少,猴子吃不飽!給全天下的老闆:加薪500是羞辱,不是激勵!
「房貸付完,房子好歹是自己的!」還有這種想法?最後會窮也是剛好而已